Figure 1-1. General View, Model HDS-E Standard Pulvi-Mixer With Asphalt Emulsion Handling SystemFigure 1-2. Number PlateFigure 1-3. Two-Stroke Cycle OperationGENERAL SPECIFICATIONSFigure 1-4. Model Number CodingFigure 1-5. Typical Engine Serial Number and Model Number as Stamped on Cylinder Block Option PlateLubrication SystemCROSS SECTION OF ENGINE MODEL VH4DShipping and LiftingService Classification of OilFigure 1-8. Operating ControlsWater Temperature GageStarter SwitchTABLE 1-1. Oil Pressures For Various EngineCooling System Figure 1-9. Hood and Rotor Assembly NomenclatureFigure 1-10. Rotor OperationFigure 1-11. Instant Depth CheckV.P.I. Fluid Handling SystemTable 1-3. Pulvi-Mixer Reference Application ChartWarm-Up PeriodFigure 1-13. Spray bar Nozzle AssemblyFigure 1-15. Wash Down SystemFigure 1-17. Standard RotorDIESEL ENGINE AND RELATED COMPONENTSMAIN VEHICLE WIRING DIAGRAMTailboard WearplateROTOR TINE REPLACEMENTROTOR AND JACK AXLE REMOVALSHEAR COUPLING REPAIR SUBSECTION 2 EMULSION PUMP AND WASH DOWN PUMPTroubleshootingSUBSECTION 2 EMULSION PUMP AND WASH DOWN PUMPHYDRAULIC BRAKE LAYOUTDISASSEMBLYBRAKE MASTER CYLINDERFigure 7. Wheel Cylinder Exploded ViewFigure 1. Sectional View of Type DPB Single Plate ClutchGENERAL DESCRIPTIONFigure 2. Checking Dimension `A'COMMON SERVICE PROBLEMSCOMMON SERVICE PROBLEMS (Cont.)CHECKING FOR MISALIGNMENTFigure 5. Knocking Out Drive Gear AssemblyFigure 8. Sectional and Exploded View of Rotor Drive transmissionFIGURE 9. Removing Drive Gear BearingFIGURE 12. Pressing on Countershaft Rear BearingTWO SPEED ROTOR DRIVE TRANSMISSIONDISASSEMBLE DRIVE UNITEXPLOSION VIEW OF UNIT HOUSING DRIVE AXLEDISASSEMBLE PINION AND CAGE ASSEMBLYCOMPLETE ASSEMBLIESREASSEMBLE PINION AND CAGE ASSEMBLYREASSEMBLE PINION AND CAGE ASSEMBLY - ContinuedASSEMBLE DIFFERENTIAL AND BEVEL GEARADJUST DIFFERENTIAL BEARING PRE-LOADTORQUE SPECIFICATIONSSUBSECTION 5 REAR AXLE ASSEMBLY AND FINAL DRIVEDISASSEMBLE PLANETARY SPIDER ASSEMBLYREMOVE THE FLOATING RING GEAR ASSEMBLYDISASSEMBLE BRAKE SHOE AND LINER ASSEMBLYWHEEL BEARING ADJUSTMENTREASSEMBLE PLANETARY SPIDER ASSEMBLYINSTALL PLANETARY SPIDER ASSEMBLYTWO SPEED NOSE BOX TRANSMISSIONTWO SPEED NOSE BOX TRANSMISSIONASSEMBLYTRACTION DRIVE AXLEDISASSEMBLE DRIVE UNITPREPARE FOR REASSEMBLYCOMPLETE ASSEMBLIESREASSEMBLE AXLEREASSEMBLE PINION AND CAGE ASSEMBLYASSEMBLE DIFFERENTIAL AND BEVEL GEARADJUST DIFFERENTIAL BEARING PRE-LOADTORQUE SPECIFICATIONSSUBSECTION 6 HYDROSTATIC PUMP AND MOTORSCHEMATIC HYDROSTATIC DRIVEHYDROSTATIC TRACTION DRIVE AND GEARING ARRANGEMENT DIAGRAMManual Displacement ControlStart Up ProcedureHYDROSTATIC PUMP AND MOTORHYDRAULIC SUPPORT SYSTEMSystem Relief ValvesMOTOR REPLACEMENTTROUBLESHOOTING GAUGE ISTALLATION AND INFORMATIONSYSTEM OPERATING HOTSYSTEM RESPONSE IS SLUGGISHInspect Manual Displacement ControlInspect Charge Check ValvesCONTROL ADJUSTMENTSCentering SpringMINOR REPAIRSShaft SealSystem Relief ValveMotor ManifoldInstallationControlFIXED DISPLACEMENT MOTORSpecial ToolsSpecial Tools - ContinuedSpecial Tools - ContinuedSpecial Tools - ContinuedSpecial Tools - ContinuedSpecial Tools - ContinuedSpecial Tools - ContinuedSpecial Tools - ContinuedVARIABLE DISPLACEMENT PUMPVARIABLE DISPLACEMENT PUMP - ContinuedVARIABLE DISPLACEMENT PUMP - ContinuedVARIABLE DISPLACEMENT PUMP - ContinuedVARIABLE DISPLACEMENT PUMP - ContinuedVARIABLE DISPLACEMENT PUMP - ContinuedVARIABLE DISPLACEMENT PUMP - ContinuedVARIABLE DISPLACEMENT PUMP - ContinuedVARIABLE DISPLACEMENT PUMP - ContinuedVARIABLE DISPLACEMENT PUMP - ContinuedVARIABLE DISPLACEMENT PUMP - ContinuedVARIABLE DISPLACEMENT PUMP - ContinuedVARIABLE DISPLACEMENT PUMP - ContinuedVARIABLE DISPLACEMENT PUMP - ContinuedVARIABLE DISPLACEMENT PUMP - ContinuedVARIABLE DISPLACEMENT PUMP - ContinuedVARIABLE DISPLACEMENT PUMP - ContinuedVARIABLE DISPLACEMENT PUMP - ContinuedINSTALLATION TORQUE VALUESSUBSECTION 7 HYDRAULIC PUMPFIGURE 4 Marking of the Gears for LocationPUMP ASSEMBLYFIGURE 12 Use of India Stone on GearsFIGURE 17 Drive Shaft, Inner Wear Plate and Seal Assembly being Installed in AdapterBREAK-IN OF REPAIRED PUMPSFIGURE 1 Valve SectionREPLACING SPOOL SEALS IN CONTROL VALVEREPLACING SPOOL SEALS IN CONTROL VALVE - ContinuedFIGURE 4 Model V20 Directional Control Valve, Typical Main AssemblyTAILBOARD HYDRAULIC CYLINDER SPRAY BAR HYDRAULIC CYLINDER SPRAY BAR HYDRAULIC CYLINDER - ContinuedSUBSECTION 10 - DIESEL ENGINESCOPE AND USE OF THE MANUALGENERAL PROCEDURESGENERAL PROCEDURES - ContinuedWORK SAFELYCONTENTSCYLINDER BLOCKFig. 2 - Cutaway View of Cylinder Block Showing Air and Water PassagesFig. 5 - Engine Mounted on Overhaul StandFig. 7 - Cleaning Cylinder BlockFig. 9 - Cylinder Block Prepared for Pressure TestFig. 10 - Honing Bore of Cylinder BlockFig. 12. Checking Bore of Cylinder BlockFig. 14. Block Bore Measurement Record FormFig. 16. Checking Top Face of Cylinder BlockFig. 18. Checking Depth of Counterbore for Cylinder Liner with Tool J 22273Assemble and Install EngineAssemble and Install Engine - ContinuedCYLINDER BLOCK END PLATESCYLINDER BLOCK END PLATES - ContinuedFig. 1. Air Box Drain TubesCYLINDER HEADFig. 3. Typical Mounting of Cylinder HeadCylinder Head MaintenanceFig. 5. Removing or Installing Injector Control TubeFig. 7. Cylinder Head Prepared for Pressure Test using Tool J 28454Non-Fluorescent Penetrant MethodFig. 9- Minimum Distance Between Top and Bottom Faces of Cylinder HeadAssemble Cylinder HeadFig. 11 Cylinder Head Seals and GasketsFig. 13 Cylinder Head Bolt Tightening SequencePre-lnstallation InspectionVALVE AND INJECTOR OPERATING MECHANISMRemove Rocker Arms and ShaftFig. 4. Cam Followers and GuideFig. 5. Cam Roller ClearancesFig. 7. Testing Cam Follower Spring using Tool J 22738-02Fig. 8. Removing or Installing Cam Follower Roller using Tool J 5840-01Fig. 11. Checking Cam Follower to GuideFig. 12. Adjusting Cam Follower GuideFig. 2. Assembly of Exhaust Valves and GuidesRemove Exhaust Valve Spring (Cylinder Head Installed)Fig. 4. Testing Exhaust Valve Spring using Tool J 22738-02Fig. 6. Removing Exhaust Valve GuideFig. 9. Removing Valve Seat InsertFig. 11. Refacing Exhaust ValveFig. 14 - Relationship Between New Exhaust Valve, Insert and Cylinder HeadFig. 16. Checking Pressure Required to Open the Exhaust Valve in Cylinder HeadInstall Engine Lifter BracketFig. 1. Typical Valve Rocker Cover Assembly (Current)Remove and Install Valve Rocker CoverFig. 1. Typical Six Cylinder Crankshaft (Former)Fig. 2. Typical Crankshaft, Timing Gear and Oil Pump Drive Gear Assembly-Four Cylinder EngineCrankshaft MeasurementsFig. 4. Critical Crankshaft Loading ZonesFig. 6. Dimensions of Crankshaft JournalsFig. 8. New or Morco Remanufactured CrankshaftFig. 10. Checking Crankshaft End PlayInstall CrankshaftFig. 1. Crankshaft Front Oil SealFig. 4. Crankshaft Rear Oil Seal MountingInstall Crankshaft Front Oil SealFig. 1. Main Bearing Shells, Bearing Caps and Crankshaft Thrust WashersFig. 4. Removing Upper Rear Main Bearing ShellFig. 5. Comparison of Main Bearing Shells MinimumFig. 8. Crankshaft Thrust Washers in PlaceFig. 9 - Main Bearing Cap MarkingFig. 1. Crankshaft Front Cover Mounting (Vibration Damper Removed)Install Crankshaft Front CoverCRANKSHAFT VIBRATION DAMPERFig. 3. Vibration Damper and Crankshaft Pulley Assembly MountingInstall Vibration Damper on CrankshaftFig. 1. Removing Rubber Mounted Pulley from Crankshaft using Tool J 5356Install Crankshaft PulleyRemove Flywheel (Transmission Removed)Remove Ring GearFig. 4. Torque - Turn LimitsCLUTCH PILOT BEARINGFig. 1. Typical Flywheel Housing MountingFig. 3. Flywheel Housing Bolt Tightening Sequence (Operation 1)Fig. 4. Flywheel Housing Bolt Tightening Sequence (Operation 2)Fig. 1. Cross-Head Piston and Connecting Rod AssemblyInspect Piston RingsFig. 5. Checking Fire Ring Groove in Piston Crown using Tool J 24599Fig. 7. Installing Piston PinFig. 9. Installing Piston Pin Retainer using Tool J 23762Fig. 11 - Measuring Piston-to-Liner Clearance using Tool J 5438-01Fig. 14 - Measuring Piston Ring GapFig. 16. Piston Ring Installation Instructions.CONNECTING RODFig. 2. Magnetic Particle Inspection Limits for Connecting Rod.Fig. 3 - Dimensional Inspection of Cross-Head Piston Connecting RodsAssemble Connecting Rod to PistonFig. 1 - Connecting Rod and Bearing ShellsInstall Connecting Rod Bearing ShellsFig. 1. Typical Cylinder Liner.Fig. 2 -Cylinder LinerFig. 6. Cylinder Liner Ridge Due to Wear.Fig. 8 - Checking Bore of Cylinder Line Using Tool J 5347-01NEW CYLINDER LINER TO NEW CYLINDER BLOCK BORE FITSFig. 9. Cylinder Liner ClassificationFig. 11. Checking Distance of Liner Flange Below Top Face of BlockFig. 13. Typical Connecting Rod MarkingsInstall Cylinder Liner, Piston and Connecting Rod AssemblyFig. 2. Loosening Nut on Camshaft or BalanceInstall Front Balance WeightsFig. 1. Gear Train and Timing Marks-Right-Hand Rotation Engine (Standard Timing Shown)Fig. 2. Pointer Installation for Marking Top-Dead-CenterFig. 3. Checking Engine Timing By Measuring Injector DepressionFig. 1. Camshaft and Balance Shaft AssembliesFig. 2. Woodruff Keys for Current CamshaftsFig. 5. Removing or Installing Shaft Bearing Retainer BoltsFig. 7. Removing Gear (Camshaft or Balance Shaft Gear Puller J 1902-01)Fig. 9. Camshaft and Balance Shaft Journal FilletsFig. 10. Typical Camshaft and Balance Shaft Details and Relative Location of PartsFig. 11. Comparison of End Bearings and Thrust WashersFig. 12. Camshaft Plug InstallationFig. 13. Camshaft Intermediate Bearing Lock ScrewsFig. 2. Removing Gear (Camshaft or Balance Shaft)Fig. 3. Replacing Gear (Camshaft Shown)Fig. 1. Idler Gear Mounting Typicalig. 2. Pressing Hub Out of BearingFig. 4. Idler Gear Details and Relative Location of PartsFig. 6. Fixture for Testing Bearing Pre-LoadFig. 8. Checking Pre-Load of Idler Gear BearingInstall Idler Gear, Hub and Bearing AssemblyFig. 1. Removing Crankshaft Timing GearFig. 1. Typical Blower Drive Gear and Support AssemblyFig. 4. Bower Drive Shaft MountingFig. 5. Typical Blower Drive Gear Details and Relative Location of PartsFig. 6. Inserting Blower Drive CamFig. 1. Typical Components of Accessory Drive For Direct-Driven AccessoriesACCESSORY DRIVEFig. 1. Balance Weight Cover MountingCHECKING BEARING CLEARANCESTROUBLE SHOOTINGTABLE OF SPECIFICATIONS, NEW CLEARANCES AND WEAR LIMITSTABLE OF SPECIFICATIONS, NEW CLEARANCES AND WEAR LIMITS - ContinuedTABLE OF SPECIFICATIONS, NEW CLEARANCES AND WEAR LIMITS - ContinuedTABLE OF SPECIFICATIONS, NEW CLEARANCES AND WEAR LIMITS - ContinuedTABLE OF SPECIFICATIONS, NEW CLEARANCES AND WEAR LIMITS - ContinuedSTANDARD BOLT AND NUT TORQUE SPECIFICATIONSuEXCEPTIONS TO STANDARD BOLT AND NUT TORQUE SPECIFICATIONSSTANDARD PIPE PLUG TORQUE SPECIFICATIONSSPECIAL PLUG TORQUE SPECIFICATIONSSERVICE TOOLSSERVICE TOOLS - ContinuedFig. 1. Schematic Diagram of Typical Fuel SystemFig. 2. Cutaway View of Fuel InjectorFig. 3 Fuel Metering from No-Load to Full-LoadFig. 6 Fuel Injector MountingFig. 9. Removing Injector Follower Stop PinFig. 11. Injector Tester J 23010 Clamping HeadsFig. 12. Injector Installed in Tester J 23010 with clamping HeadVisual Inspection of PlungerFig. 15. Adaptor and Tube Assembly on Injector Tester J 23010Unclamping the InjectorFig. 16. Checking Needle Valve LiftFig. 17 - Injector Needle Valve Tester J 23010 with Auxiliary Tester J 22640Fig. 20 - Position of Calibrator Fuel Flow PipesFig. 22 Setting Calibrator Stroke CounterFig. 27. Cleaning injector Spray TipFig. 31. Sealing Surfaces which may Require LappingFig. 34. Location of Filter in Injector BodyFig. 36. Injector Rack, Gear, Spray Tip and Valve Assembly Details and Relative Location of PartsFig. 37. Injector Plunger, Follower and Relative Location of PartsFig. 39. Spray Tip Sealing Surface IdentificationFig. 42. Installing Injector Follower Stop PinFig. 43. Checking Injector Spray Tip Concentricity using Tool J 29584Check Spray Tip ConcentricityInstall InjectorInstall Injector TubeFig. 3 - Upsetting Injector TubeFig. 5 - Reaming Injector Tube for Injector NutReam Injector TubeFig. 1 - Typical Fuel Pump AssemblyFig. 2 - Typical Fuel Pump Mounting and DriveFig. 3 - Fuel Pump Valving and Rotation (Right-Hand Pump)Fig. 5 - Removing Pump CoverFig. 7 - Fuel Pump Details and Relative Location of PartsFig. 9 - Installing Outer Oil SealFig. 10 Installing Drive Shaft and Gear AssemblyFig. 1 - Typical Spin-On Filter MountingFig. 1 - Cylinder Head with Integral Fuel ManifoldsMECHANICAL GOVERNORRemove GovernorFig. 1 - Variable Speed Mechanical GovernorFig. 2 - Variable Speed Governor MountingFig. 5 Governor Control Housing Details and Relative Location of PartsFig. 7. Removing Operating Shaft from Operating ForkFig. 9. Governor Weight Housing Details and Relative Location of PartsFig. 11 Installing Needle Bearing in Governor Cover using Tool J 21068Fig. 12. Cross Section of Governor Variable Speed Spring HousingFig. 13. Variable Speed Spring Housing and Shaft Details and Relative Location of PartsFig. 15. Governor Weight HousingInstall GovernorFUEL INJECTOR CONTROL TUBEInstall Injector Control TubeFig. 1. Checking Fuel OutputREFINISH LAPPING BLOCKSEFFECT OF PRE-IGNITION ON FUEL INJECTORREFINISHING INJECTOR FOLLOWER FACEPRESSURIZE FUEL SYSTEM CHECK FOR LEAKSCHECKING FUEL FLOWCHECKING FUEL FLOW - ContinuedSHOOTING CHARTS (Needle Valve Injectors)SHOOTING CHARTS (Needle Valve Injectors) - ContinuedSHOOTING CHARTS (Needle Valve Injectors) - ContinuedSTANDARD BOLT AND NUT TORQUE SPECIFICATIONSEXCEPTIONS TO STANDARD BOLT AND NUT TORQUE SPECIFICATIONSSERVICE TOOLSSERVICE TOOLS - ContinuedFig. 1 - Air Flow Through Blower and EngineAir Cleaner MountingFig. 1 - Dry Type Air Cleaner (Heavy Duty)ServiceAIR SHUTDOWN HOUSINGFig. 2 - Air Shutdown Housing Mounting and Bolt LocationBLOWERFig. 1 - Blower and Drive Assembly and Accessories including Mechanical Governor Attached to blowerFig. 2 Typical Blower Mounting (71 Engine)Fig. 4 Removing Blower Rotor Gears from Blower Rotor Shafts with Tool Set J 6270-FFig 5 - Removing Blower End Plate using Tool Set J 6270-FFig. 7 - Typical Details and Relative Location of PartsFig. 8 - Installing Oil Seal in Blower End Plate using Tool J 6270-3.Fig. 10 - Position of Blower Front End Plate on HousingFig. 13 - Installing Roller Bearing on Rotor Shaft and in Front End Plate using Tool J 6270-4.Fig. 14 - Installing Ball Bearing on Rotor Shaft and in Rear End Plate using Tool J 6270-7.Fig. 16 - Measuring "CC" and "C" Clearances Between Blower Rotor Lobes.Fig. 17 - Chart of Minimum Clearances for Blowers.Fig. 18 - Diagram Showing Proper Location of Shims for Correct Rotor Lobe Clearances.Attach Accessories to BlowerFig. 1 - Removing Rotor Stub Shaft.Install Service Rotor Front Stub ShaftTABLE OF SPECIFICATIONS, NEW CLEARANCES AND WEAR LIMITSSTANDARD BOLT AND NUT TORQUE SPECIFICATIONSEXCEPTIONS TO STANDARD BOLT AND NUT TORQUE SPECIFICATIONSSERVICE TOOLSLUBRICATION SYSTEMFig. 1 - Schematic Diagram of Typical Lubrication System.Fig. 2 - Blower Lubrication.Fig. 1 - Oil Pump Assembly.Fig. 2 - Typical Oil Pump Mounting.Fig. 3 - Oil Pump Details and Relative Location of Parts.Fig. 5 - Removing Oil Pump Drive Gear form Shaft.Fig. 6 - Diameter and Location of Bushing in Oil Pump.Fig. 8 - Removing Oil Pump Driving Gear from CrankshaftFig. 9 - Installing Oil Pump Driving Gear on CrankshaftInstall Oil Pump Driving Gear on CrankshaftFig. 1 - Lubricating Oil Pressure Regulator Details and Relative Location of Parts.Assemble Oil Pressure RegulatorFig. 1 - Typical Oil Filter Mounting.Fig. 3- Bypass ValveFigure 1. Typical Lubricating Oil Cooler Mounting-Radiator Cooled EngineFig. 2 Oil Cooler Core Prepared for Pressure CheckInstall Lubricating Oil CoolerLUBRICATING OIL COOLER BYPASS VALVEFigure 1. Typical Dipstick MountingFigure 1. Typical Deep Sump Type Oil PanFigure 1. Breather Mounted on Cylinder BlockSTANDARD BOLT AND NUT TORQUE SPECIFICATIONSEXCEPTIONS TO STANDARD BOLT AND NUT TORQUE SPECIFICATIONSSERVICE TOOLSRADIATOR AND COOLING FANFig. 1 - Typical Cooling System with Radiator and FanCooling System CapacityMiscellaneous Cooling SystemLUBRICATION SYSTEMFig. 1 - Water Pump With Ceramic Insert in ImpellerFig. 4 Pressing Pump Shaft from ImpellerFig. 6 - Water Pump Details and Relative Location of PartsFig. 7 - Installing Pump ImpellerFig. 1 - Typical Water Manifold Mounting Industrial UnitFig. 1 - Typical thermostat Housing Mounting (Radiator Cooling System)Fig. 2 - Method of Checking Thermostat OperationCleaning RadiatorFig. 1 Removing Radiator, Shell and Shroud with Lifting Hook (Typical)COOLANT PRESSURE CONTROL CAPFig. 1 . Typical Fan and Fan Hub AssemblyFig. 2 - Shaft Type Fan Hub Assembly Details for Compact Front End Engine.Fig. 3 - Shaft Type Fan Hub Assembly.STANDARD BOLT AND NUT TORQUE SPECIFICATIONSEXCEPTIONS TO STANDARD BOLT AND NUT TORQUE SPECIFICATIONSEXHAUST SYSTEMFig. 1 - Typical Air-Cooled Exhaust Manifold Mounting.Remove Exhaust ManifoldELECTRICAL SYSTEMFig.1 - Hinge-Mounted Alternator.Fig. 4 - Terminal Connections.Fig. 6 - Charging Circuit.ABNORMAL CHARGING SYSTEM OPERATIONFig. 10 - Testing Diode Trio.Fig. 11 - Testing Rectifier Bridge.Fig. 13 - Drive End Bearing Assembly.Fig. 16 - Tighten Alternator Pulley Retaining NutFig. 17 - Battery Connecting Diagram.Battery Safety PrecautionsFig. 2 - Cross-section of Starting Motor with Sprag Heavy-Duty Clutch Drive.TROUBLESHOOTINGInterpreting Results of TestsFig. 5 - Checking Solenoid Hold-In Winding.Fig. 6 - Checking Solenoid Pull-In Winding.Fig. 8 - Measuring Pinion Clearance.Fig. 1 - Typical Instrument Panel.Fig. 3 - Tachometer Mounting.Fig. 5 - Tachometer Head.MANUAL SHUTDOWN SYSTEMCOLD WEATHER STARTINGALIGNMENT TOOLS FOR TACHOMETER DRIVE COVERS AND ADAPTORSSTANDARD BOLT AND NUT TORQUE SPECIFICATIONSEXCEPTIONS TO STANDARD BOLT AND NUT TORQUE SPECIFICATIONSSERVICE TOOLSENGINE OPERATING CONDITIONSDYNAMOMETER TEST AND RUN-IN PROCEDURESDynamometerENGINE TEST REPORTBASIC RUN-IN INSPECTIONINSPECTION AFTER FINAL RUN-INFUEL OILS FOR DETROIT DIESEL ENGINESDIESEL FUEL LINE DE-ICERLUBRICATING OILS FOR DETROIT DIESEL ENGINESUSED LUBE OIL ANALYSIS PROGRAMLUBE OIL FILTER CHANGE INTERVALSTATEMENT OF POLICY ON FUEL AND LUBRICANT ADDITIVESCOOLANT REQUIREMENTSFig. 1 - Heat Transfer CapacityFig. 2 Coolant Freezing and Boiling Temperatures vs. Antifreeze Concentration (Sea Level)GENERAL RECOMMENDATIONSGENERAL RECOMMENDATIONS - ContinuedENGINE TUNE-UP PROCEDURESFig. 1 - Adjusting Valve Clearance (Two Valve Head)Fig. 1 - Timing Fuel InjectorFig. 1 - Adjusting Governor CapFig. 3 - Buffer and Idle Speed Adjusting ScrewFig. 6 - Location of Stops and ShimsAdjust Booster SpringPREVENTIVE MAINTENANCE TROUBLE SHOOTING - STORAGE - PLUGGING CHARTSENGINE OIL CHANGE INTERVALSDiesel Fuel ContaminationThrottle and Clutch ControlsExhaust SystemEngine and Transmission MountsCrankcase BreatherFig. 1 - Locating a Misfiring CylinderFig. 2 - Checking Compression PressureFig. 3 - Inspecting Piston RingsPROPER USE OF MANOMETERPRESSURE CONVERSION CHARTEXHAUST SMOKE ANALYSISEXHAUST SMOKE ANALYSIS - ContinuedHARD STARTINGHARD STARTING - ContinuedABNORMAL ENGINE OPERATIONABNORMAL ENGINE OPERATION - ContinuedNO FUEL OR INSUFFICIENT FUELNO FUEL OR INSUFFICIENT FUEL - ContinuedABNORMAL ENGINE COOLANT OPERATING TEMPERATUREEXCESSIVE CRANKCASE PRESSURELOW OIL PRESSURELOW OIL PRESSURE- CONTINUEDHIGH LUBRICATING OIL CONSUMPTIONHIGH LUBRICATING OIL CONSUMPTION - CONTINUEDPREPARING ENGINE FOR STORAGEPROCEDURE FOR RESTORING AN ENGINE TO SERVICE WHICH HAS BEEN IN EXTENDED STORAGEPLUGGING CHARTS - LC and RC ENGINESPLUGGING CHARTS - LC and RC ENGINES - ContinuedSUBSECTION 11 FRONT AXLE AND STEERINGINSTALLATION AND OPERATIONHYDRAULIC FLUID RECOMMENDATIONSTABLE II - TROUBLE SHOOTING CHARTTABLE II. - TROUBLE SHOOTING CHART (CONTINUED)Control Valve Sub-Assembly STEERING GEAR REPLACEMENTFRONT AXLE REPAIRSUBSECTION 12 STEERING CYLINDERPOWER STEERING VALVE UNIT ON STEERING COLUMNSUBSECTION 13 V.P.I. FLUID HANDLING SYSTEMCALIBRATING THE V.P.I. SYSTEM-METER RECORDING UNITCALIBRATING THE V.P.I. SYSTEM-METER RECORDING UNIT - ContinuedTRAVEL SPEED UNITPROPORTIONING SYSTEM UNITSUGGESTED EXTERNAL POWER SOURCE CIRCUITRYV.P.I. TROUBLE SHOOTINGSUBSECTION 14 GASOLINE PUMP ENGINEMAGNETO BREAKER POINT ADJUSTMENTFIGURE 6. MAGNETO TIMING DIAGRAMFIGURE 7. WIRING DIAGRAMTROUBLES CAUSES AND REMEDIESENGINE SURGES OR GALLOPSTESTING REBUILT ENGINECARBURETOR AND MANIFOLDIDLER GEAR AND SHAFTPISTONS and CONNECTING RODS CYLINDER BLOCKSVALVE TAPPETSGOVERNOR ADJUSTMENTWALBRO CARBURETORFIGURE 30. FLOAT SETTINGFIGURE 31. EXPLODED VIEW Instructions and Service Parts IllustrationLUBRICATION CHART 1 - GENERALLUBRICATION CHART 1 - GENERAL (Continued)LUBRICATION CHART 2 - EMULSION HANDLING SYSTEMFIG. 1. ROTOR HOOD, TAILBOARD, LIFT ARMS, HOOD ARMS, JACK AXLE ARMR AND SKISROTOR HOOD-CRANE-TAILBOARD-LIFT ARMS - HOOD ARMS-JACK AXLE ARMS & SKIS - REX SELF-PROPELLED PULVI MIXERSROTOR ASSEMBLY WITH SOLID TUBE AND BEYEL EDGE TINES REX ASSEMBLY NO. 602.2720, COMPLETEFIG. 3. ROTOR DRIVE CHAIN CASE (LEFT AND RIGHT REQUIRED)ROTOR DRIVE CHAIN CASEFIG. 4. ROTOR DRIVE LINEROTOR DRIVELINESFIG. 5. EMULSION PUMP ASSEMBLY PEABODY - BARNES MODELS: 30CCG, 30CCG-1, 30CCG-2EMULSION PUMP ASSEMBLYFIG. 6. PUMP FOR WASH-DOWN SYSTEMFIG. 7. EMULSION HANDLING UNIT PIPING, CONTROLS HYDRAULIC LINES AND FITTINGSEMULSION HANDLING UNIT PIPING - CONTROLS - HYDRAULIC LINES & FITTINGSEMULSION HANDLING UNIT PIPING - CONTROLS - HYDRAULIC LINES & FITTINGS - ContinuedEMULSION HANDLING UNIT PIPING - CONTROLS - HYDRAULIC LINES & FITTINGS - ContinuedFIG. 8. FLOW METERFLOW METER AND TACHOMETER GENERATOR ASSY. 4' MODEL 4MLFT- SGHFLOW METER AND TACHOMETER GENERATOR ASSY. 4' MODEL 4MLFT- SGHFIG. 9. WATER AND ASPHALT SPRAY BARS AND ROTOR HOOD COVERSWATER AND ASPHALT SPRAY BARS AND ROTOR HOOD COVERS REX SELF PROPELLED PULVI MIXERSFIG. 10. TRACTION DRIVE WHEEL ENDS AND BRAKESTRACTION DRIVE WHEEL ENDS INCLUDED IN AXLE ASSEMBLY 102-6168-1 ROCKWELL MODEL TA-279-HXI EFFECTIVE HK-381TRACTION DRIVE WHEEL ENDS INCLUDED IN AXLE ASSEMBLY 102-6168-1 ROCKWELL MODEL TA-279-HXI EFFECTIVE HK-381 - ContinuedFIG. 11. TWO SPEED TRANSMISSION - ROTOR DRIVEROTOR DRIVE TWO-SPEED TRANSMISSION REX PART NO. 602-10224-2 ROTOR DRIVE CLUTCH ASSEMBLYROTOR DRIVE TWO-SPEED TRANSMISSION REX PART NO. 602-10224-2 ROTOR DRIVE CLUTCH ASSEMBLY - ContinuedFIG. 12. TRACTION DRIVE TRANSMISSION (2 SPEED)TRACTION DRIVE TWO-SPEED TRANSMISSION INCLUDED IN AXLE ASSEMBLY 102-11053-1FIG. 13. TRACTION DRIVE AXLEDIFFERENTIAL, CASE AND HOUSING INCLUDED IN AXLE ASSEMBLY 102-11053-1FIG. 14. ROTOR DRIVE AXLEROTOR DRIVE AXLE ROCKWELL STANDARD MODEL JH-150-X-48 DWG. 35-1019ROTOR DRIVE AXLE ROCKWELL STANDARD MODEL JH-150-X-48 DWG. 35-1019ROTOR DRIVE AXLE ROCKWELL STANDARD MODEL JH-150-X-48 DWG. 35-1019LEFT HAND ROTATION TRACTION DRIVE HYDROSTATIC PUMPHYDROSTATIC PUMP - TRACTION DRIVE UNIVERSAL JOINT & CONNECTIONS TO PUMP AND ENGINE PUSH PULL UNIT - FORWARD - REVERSE NEUTRAL START SWITCHFIG. 17. TRACTION DRIVE MOTORFIG. 18. TRACTION DRIVE HYDRAULIC LINESHYDRAULIC LINES & FITTINGS - TRACTION DRIVE WHEELS & TIRES REX HYDROSTATIC DRIVE PULVI MIXERHYDRAULIC LINES & FITTINGS - TRACTION DRIVE WHEELS & TIRES REX HYDROSTATIC DRIVE PULVI MIXER - ContinuedFIG. 19. HYDRAULIC PUMP FOR TAILBOARD - SPRAY BAR AND CRANE RAMSFIG. 20. HYDRAULIC CONTROL VALVE FOR TAILBOARD AND ROTOR LIFT RAMSHYDRAULIC CONTROL VALVE FOR ROTOR HOIST RAM AND TAILBOARD CONTROL RAM (GRESEN MFG. CO. "CP4" - 2 SPOOL)FIG. 21. MODEL V20 DIRECTIONAL CONTROL VALVE TYPICAL MAIN ASSEMBLYFIG. 22. 4-WAY, 3-POSITION VALVE SECTIONFIG. 23. STANDARD SPOOL POSITIONERFIG. 25. OPTIONAL VERTICAL HANDLE AND BRACKET ASSEMBLYFIG. 26. LOAD CHECK PLUG ASSEMBLYFIG. 27. MODEL RDSON MAIN RELIEF VALVE (NON-ADJUSTABLE)Standard Buna-N Seals and O-RingsFIG. 28. HYDRAULIC LINES - VALVE TO SPRAY BARFIG. 29. HYDRAULIC LINES SCHEMATIC FOR ROTOR AND TAILBOARDHYDRAULIC LINES SCHEMATIC ROTOR & TAILBOARD LIFT FOR G.M. DIESEL POWER ONLY REX DWG. NO. 602-2750FIG. 30. HYDRAULIC CYLINDER FOR SPRAY BAR AND FIFTH WHEELFIG. 31. HYDRAULIC CYLINDER RAM FOR ROTOR LIFTFIG. 32. HYDRAULIC CYLINDER FOR SPRAY BAR AND FIFTH WHEELFIG. 33. HYDRAULIC CYLINDER FOR TAILBOARDFIG. 34. GENERAL MOTORS DIESEL POWER UNITGENERAL MOTORS DIESEL POWER UNIT - CONTINUEDGENERAL MOTORS DIESEL POWER UNIT - CONTINUEDGENERAL MOTORS DIESEL POWER UNIT - CONTINUEDFIG. 35. POWER STEERING PUMPFIG. 36. POWER STEERING CYLINDERPOWER STEERING CYLINDER ASSEMBLY ROSS GEAR DIVISION PART NO. C36531-A4-50 REX PART NO. 102-8404-1FIG. 37. FIFTH WHEEL - TACH DRIVEFIFTH WHEEL -- GEARCASE - GENERATOR VISUAL PERFORIMANCE INDICATORFIFTH WHEEL -- GEARCASE - GENERATOR VISUAL PERFORIMANCE INDICATOR - ContinuedFIG. 38. EXPLODED VIEW OF ENGINEFIG. 39. MANIFOLD AND CRANKCASE GROUPMANIFOLD AND CRANKCASE GROUPFIG. 40. CRANKSHAFT, PISTON AND CONNECTING ROD GROUPCRANKSHAFT, PISTON AND CONNECTING ROD GROUPFIG. 41. CAMSHAFT AND FUEL PUMP MOUNTING GROUPFIG. 42. OIL FILTER AND OIL FILLER MOUNTING GROUPFIG. 43. AIR SHROUDINGFIG. 44. CYLINDER BLOCK ASSEMBLYFIG. 45. MAGNETO AND GEAR COVER GROUPFIG. 46. K 95 L Oil Pump AssemblyFIG. 47. T 89K-S1, GOVERNOR ASSEMBLYFIG. 48. TT-45-L AND TT-45L-1 GOVERNOR CONTROL ASSEMBLIESFIG. 50. Q12J GASKET SETFIG. 50. STARTING MOTOR ASSEMBLY WITH FOLO-THRU BENDIXFIG. 51. STARTER MOUNTINGFig. 52. YC66D-S1 HIGH TEMP. SAFETY SWITCH KIT.Fig. 53. WALBRO CARBURETOR MODEL LUB.WALBRO CARBURETORFig. 54. LO-64 SIDE MOUNT AIR CLEANER ASSEMBLY.Fig. 55. MAGNETO - Fairbanks-Morse No. FM-XZE4B7-4, Wisconsin Motor No. Y-98-C-S2 per MIL-E-11275-C SpecificationsFig. 55. MAGNETO (Cont.)Fig. 55. MAGNETO (Cont.)FIG. 56. FRONT AXLE ASSEMBLY.FRONT AXLE - FRONT AXLE KIT 102-9438-1 - ROCKWELL STANDARD #FC-901FIG. 57. CONTROLS.FIG. 57. CONTROLS. - ContinuedFIG. 57. CONTROLS. - ContinuedFIG. 57. CONTROLS. - ContinuedFIG. 58. MAIN FRAME, ENGINE HOUSE, FLOORBOARD AND FENDERS.MAIN FRAME - ENGINE HOUSE - FLOORBOARD- FENDERSMAIN FRAME - ENGINE HOUSE - FLOORBOARD- FENDERS - ContinuedFUEL TANK - SUCTION & RETURN FUEL LINES OPERATOR'S SEAT - TOOL BOXDECALS AND LABELS REX SELF PROPELLED PULVI MIXERWIRING SCHEMATIC - LIGHTINGINDEXINDEX - ContinuedTABLE OF CONTENTSTable of Contents (Continued)SUBSECTION I - GENERALLoad ClassificationSUBSECTION II. MAINTENANCEShipment and StorageSUBSECTION III. REPAIR PARTS SUPPLYRequisitioning Repair PartsAPPENDIX A. EQUIPMENT PUBLICATIONSAPPENDIX B. WARRANTY GUIDELINESAPPENDIX B. WARRANTY GUIDELINES - ContinuedAPPENDIX C. MAINTENANCE ALLOCATION CHARTAPPENDIX C. MAINTENANCE ALLOCATION CHART - ContinuedAPPENDIX C. MAINTENANCE ALLOCATION CHART - ContinuedSection II. MAINTENANCE ALLOCATION CHARTSection II. MAINTENANCE ALLOCATION CHART - ContinuedSection II. MAINTENANCE ALLOCATION CHART - ContinuedSection II. MAINTENANCE ALLOCATION CHART - ContinuedSection II. MAINTENANCE ALLOCATION CHART - ContinuedSection II. MAINTENANCE ALLOCATION CHART - ContinuedSection II. MAINTENANCE ALLOCATION CHART - ContinuedSection II. MAINTENANCE ALLOCATION CHART - ContinuedSection II. MAINTENANCE ALLOCATION CHART - ContinuedSection II. MAINTENANCE ALLOCATION CHART - ContinuedSection II. MAINTENANCE ALLOCATION CHART - ContinuedSection II. MAINTENANCE ALLOCATION CHART - ContinuedSection II. MAINTENANCE ALLOCATION CHART - ContinuedSection II. MAINTENANCE ALLOCATION CHART - ContinuedSection II. MAINTENANCE ALLOCATION CHART - ContinuedSection II. MAINTENANCE ALLOCATION CHART - ContinuedSECTION III - TOOL AND TEST EQUIPMENT REQUIREMENTSSECTION III - TOOL AND TEST EQUIPMENT REQUIREMENTS - ContinuedSection IV RemarksCCE MANUFACTURER FIELD CAMPAIGNS AND MODIFICA-ION PROCEDURESBASIC ISSUE ITEMS LISTAPPENDIX G. INITIAL RECOMMENDATION - PRESCRIBED LOAD LIST (PLL) - AUTHORIZED STOCKAGE LIST (ASL)APPENDIX G. INITIAL RECOMMENDATION - PRESCRIBED LOAD LIST (PLL) - AUTHORIZED STOCKAGE LIST (ASL) - ContinuedMAINTENANCE AND OPERATING SUPPLY LISTMAINTENANCE AND OPERATING SUPPLY LIST - ContinuedREQUISITION PROCESSING GENERAL INSTRUCTIONSRequisition FormatNON-NSN REQUISITION FORMATPREVENTATIVE MAINTENANCE CHECKS AND SERVICES (PMCS)OPERATOR/CREW AND ORGANIZATIONAL MAINTENANCE CHECKS AND SERVICES.OPERATOR/CREW AND ORGANIZATIONAL MAINTENANCE CHECKS AND SERVICES. - ContinuedOPERATOR /CREW PREVENTIVE MAINTENANCE CHECKS AND SERVICES (PMCS)OPERATOR /CREW PREVENTIVE MAINTENANCE CHECKS AND SERVICES (PMCS) - ContinuedOPERATOR /CREW PREVENTIVE MAINTENANCE CHECKS AND SERVICES (PMCS) - ContinuedOPERATOR /CREW PREVENTIVE MAINTENANCE CHECKS AND SERVICES (PMCS) - ContinuedORGANIZATIONAL PREVENTIVE MAINTENANCE CHECKS AND SERVICESORGANIZATIONAL PREVENTIVE MAINTENANCE CHECKS AND SERVICESORGANIZATIONAL PREVENTIVE MAINTENANCE CHECKS AND SERVICES - Continued
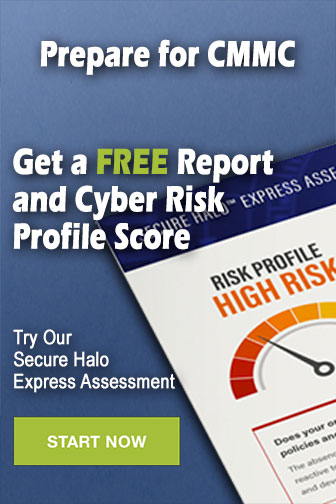