SECTION 1 OPERATIONGeneral Machine DescriptionV.P.I. Fluid Handling System - TM-5-3895-359-14-P0011GENERAL SPECIFICATIONSFigure 1-4. Model Number CodingDiesel Engine Model and Serial NumbersLubrication System - TM-5-3895-359-14-P0015CROSS SECTION OF ENGINE MODEL VH4DShipping and LiftingService Classification of OilOperation - TM-5-3895-359-14-P0019Diesel EngineStarter SwitchForward and Reverse TravelAvoid Unnecessary Engine IdlingFigure 1-9. Hood and Rotor Assembly NomenclatureFigure 1-10. Rotor OperationShear Coupling V.P.I. Fluid Handling System - TM-5-3895-359-14-P0027Table 1-3. Pulvi-Mixer Reference Application Chart.Warm-Up PeriodFigure 1-13. Spray bar Nozzle AssemblyWash Down System TinesVEHICLE SYSTEMS AND RELATED MAINTENANCE SECTION SCHEMATICMAIN VEHICLE WIRING DIAGRAMSECTION 2 - MAINTENANCEROTOR TINE REPLACEMENTCHAIN ADJUSTMENT, END DRIVE CASESHEAR COUPLING REPAIRSUBSECTION 2 EMULSION PUMP AND WASH DOWN PUMPTroubleshootingSUBSECTION 2 EMULSION PUMP AND WASH PUMPSUBSECTION 3 BRAKESDISASSEMBLY - TM-5-3895-359-14-P0043BRAKE MASTER CYLINDERBRAKE SYSTEM BLEEDINGSUBSECTION 4 - ROTOR DRIVEGENERAL DESCRIPTIONFigure 2. Checking Dimension `COMMON SERVICE PROBLEMSCOMMON SERVICE PROBLEMS (Cont.)CHECKING FOR MISALIGNMENTTWO SPEED ROTOR DRIVE TRANSMISSIONFigure 8. Sectional and Exploded View of Rotor Drive transmissionFIGURE 9. Removing Drive Gear BearingFIGURE 12. Pressing on Countershaft Rear BearingTWO SPEED ROTOR DRIVE TRANSMISSION (Cont)ROTOR DRIVE AXLEExplosion View Of Unit Type Housing Drive Axle - TM-5-3895-359-14-P0058DISASSEMBLE PINION AND CAGE ASSEMBLYROUGH PARTSREASSEMBLE AXLE - TM-5-3895-359-14-P0061REASSEMBLE PINION AND CAGE ASSEMBLY - TM-5-3895-359-14-P0062ASSEMBLE DIFFERENTIAL AND BEVEL GEAR - TM-5-3895-359-14-P0063ADJUST DIFFERENTIAL BEARING PRE-LOAD - TM-5-3895-359-14-P0064CHECK AND ADJUST GEAR LASH - TM-5-3895-359-14-P0065PREPARE FOR REMOVALREMOVE PLANETARY SPIDER ASSEMBLYREMOVE THE FLOATING RING GEAR ASSEMBLYDISASSEMBLE BRAKE SHOE AND LINER ASSEMBLYWHEEL BEARING ADJUSTMENTREASSEMBLE PLANETARY SPIDER ASSEMBLYINSTALL PLANETARY SPIDER ASSEMBLYTWO SPEED NOSE BOX TRANSMISSION - TM-5-3895-359-14-P0073TWO SPEED NOSE BOX TRANSMISSION - TM-5-3895-359-14-P0074ASSEMBLYExplosion View of unit Type Housing Drive Axle - TM-5-3895-359-14-P0076DISASSEMBLE DRIVE UNITPREPARE FOR REASSEMBLYCORROSION PREVENTIONREASSEMBLE AXLE - TM-5-3895-359-14-P0080REASSEMBLE PINION AND CAGE ASSEMBLY - TM-5-3895-359-14-P0081ASSEMBLE DIFFERENTIAL AND BEVEL GEAR - TM-5-3895-359-14-P0082ADJUST DIFFERENTIAL BEARING PRE-LOAD - TM-5-3895-359-14-P0083CHECK AND ADJUST GEAR LASH - TM-5-3895-359-14-P0084SUBSECTION 6 HYDROSTATIC PUMP AND MOTORSchematic Hydrostatic Drive HYDROSTATIC TRACTION DRIVE AND GEARING ARRANGEMENT DIAGRAMMAINTENANCE INFORMATIONFluidsBASIC OPERATIONHYDRAULIC SUPPORT SYSTEMSystem Relief ValvesInstructionsTrouble Shooting Gauge Installation and Information System Operating HotSystem Will Not Operate in Either Direction Inspect Manual Displacement ControlInspect Charge Check ValvesCONTROL ADJUSTMENTSCentering SpringMINOR REPAIRSShaft SealManifold Assembly ComponentsMotor ManifoldInstallationControlMAJOR REPAIRS - TM-5-3895-359-14-P0107FIXED DISPLACEMENT MOTOR FIXED DISPLACEMENT MOTOR (Cont) - TM-5-3895-359-14-P0109FIXED DISPLACEMENT MOTOR (Cont) - TM-5-3895-359-14-P0110FIXED DISPLACEMENT MOTOR (Cont) - TM-5-3895-359-14-P0111FIXED DISPLACEMENT MOTOR (Cont) - TM-5-3895-359-14-P0112FIXED DISPLACEMENT MOTOR (Cont) - TM-5-3895-359-14-P0113FIXED DISPLACEMENT MOTOR (Cont) - TM-5-3895-359-14-P0114FIXED DISPLACEMENT MOTOR (Cont) - TM-5-3895-359-14-P0115MAJOR REPAIRS - TM-5-3895-359-14-P0116VARIABLE DISPLACEMENT PUMP VARIABLE DISPLACEMENT PUMP (Cont) - TM-5-3895-359-14-P0118VARIABLE DISPLACEMENT PUMP (Cont) - TM-5-3895-359-14-P0119VARIABLE DISPLACEMENT PUMP (Cont) - TM-5-3895-359-14-P0120VARIABLE DISPLACEMENT PUMP (Cont) - TM-5-3895-359-14-P0121VARIABLE DISPLACEMENT PUMP (Cont) - TM-5-3895-359-14-P0122VARIABLE DISPLACEMENT PUMP (Cont) - TM-5-3895-359-14-P0123VARIABLE DISPLACEMENT PUMP (Cont) - TM-5-3895-359-14-P0124VARIABLE DISPLACEMENT PUMP (Cont) - TM-5-3895-359-14-P0125VARIABLE DISPLACEMENT PUMP (Cont) - TM-5-3895-359-14-P0126VARIABLE DISPLACEMENT PUMP (Cont) - TM-5-3895-359-14-P0127VARIABLE DISPLACEMENT PUMP (Cont) - TM-5-3895-359-14-P0128VARIABLE DISPLACEMENT PUMP (Cont) - TM-5-3895-359-14-P0129VARIABLE DISPLACEMENT PUMP (Cont) - TM-5-3895-359-14-P0130VARIABLE DISPLACEMENT PUMP (Cont) - TM-5-3895-359-14-P0131VARIABLE DISPLACEMENT PUMP (Cont) - TM-5-3895-359-14-P0132VARIABLE DISPLACEMENT PUMP (Cont) - TM-5-3895-359-14-P0133INSTALLATION TORQUE VALUESSUBSECTION 7 HYDRAULIC PUMPFIGURE 3 Exploded View of Hydraulic PumpPUMP ASSEMBLYFIGURE 14 Wear Plate Seating CheckFIGURE 17 Drive Shaft, Inner Wear Plate and Seal Assembly being Installed in AdapterBREAK-IN OF REPAIRED PUMPSSUBSECTION 8 HYDRAULIC CONTROL VALVESREPLACING SPOOL SEALS IN CONTROL VALVEREPLACING SPOOL SEALS IN CONTROL VALVE (Cont)REPLACING CENTER SECTION ASSEMBLIES IN THE VALVESUBSECTION 9 HYDRAULIC CYLINDERSSPRAY BAR HYDRAULIC CYLINDERSPRAY BAR HYDRAULIC CYLINDER (Cont)CHAPTER 1: GENERAL INFORMATIONGENERAL PROCEDURESINSPECTION - TM-5-3895-359-14-P0151WORK SAFELYCHAPTER 2: EngineCYLINDER BLOCKENGINE AND ROTOR TRANSMISSION REMOVALRemovalClean Cylinder BlockPressure TestFig. 10 - Honing Bore of Cylinder BlockInspect Cylinder BlockFig. 14. Block Bore Measurement Record FormFig. 16. Checking Top Face of Cylinder BlockFig. 17. Minimum Distance from Center Line of Crankshaft to Top of Cylinder BlockAssemble and Install EngineAssemble and Install Engine (Cont)CYLINDER BLOCK END PLATESInstall End PlatesInspection - TM-5-3895-359-14-P0168CYLINDER HEADFig. 2. Typical Mounting of Cylinder HeadCylinder Head MaintenanceFig. 6. Cylinder Head Mounted on Holding PlatesDisassemble Cylinder HeadPressure Check Method:Fig. 9- Minimum Distance Between Top and Bottom Faces of Cylinder HeadAssemble Cylinder HeadFig. 11 Cylinder Head Seals and GasketsFig. 13 Cylinder Head Bolt Tightening SequenceInstall Cylinder HeadVALVE AND INJECTOR OPERATING MECHANISMService - TM-5-3895-359-14-P0181Remove Cam Follower and Push Rod (Cylinder Head on Engine)Fig. 5. Cam Roller ClearancesInstall Cam Follower and Push RodInstall Rocker Arms and ShaftFig. 9. Valve and Injector Operating Mechanism and Relative Location of PartsFig. 12. Adjusting Cam Follower GuideEXHAUST VALVES - TM-5-3895-359-14-P0188Remove Exhaust Valve Spring (Cylinder Head Installed)Inspection - TM-5-3895-359-14-P0190Inspect Exhaust Valve Seat InsertRemove Exhaust Valve Seat InsertRecondition Exhaust Valve and Valve SeatFig. 15. Grinding Wheel Dressing Tool or Set JFig. 16. Checking Pressure Required to Open the Exhaust Valve in Cylinder HeadENGINE LIFTER BRACKETSVALVE ROCKER COVERRemove and Install Valve Rocker CoverCRANKSHAFTInspection - TM-5-3895-359-14-P0200Crankshaft MeasurementsInspection for CracksCrankshaft GrindingInstall CrankshaftFig. 10. Checking Crankshaft End PlayInstall Crankshaft (Cont)CRANKSHAFT OIL SEALSInspection - TM-5-3895-359-14-P0208Oil SealsCRANKSHAFT MAIN BEARINGSRemove Main Bearing Shells (Crankshaft in Place)Fig. 5. Comparison of Main Bearing Shells MinimumInstall Main Bearing Shells (Crankshaft in Place)Fig. 9 - Main Bearing Cap MarkingCRANKSHAFT FRONT COVERInstall Crankshaft Front CoverCRANKSHAFT VIBRATION DAMPERInspect Vibration DamperInstall Vibration Damper on CrankshaftCRANKSHAFT PULLEYInstall Crankshaft PulleyFLYWHEELInspection - TM-5-3895-359-14-P0223Fig. 4. Torque - Turn LimitsCLUTCH PILOT BEARINGFLYWHEEL HOUSINGInstall Flywheel HousingFig. 5. Checking Flywheel Housing ConcentricityCROSS-HEAD TYPE PISTONInspect Piston RingsInspection - TM-5-3895-359-14-P0231Assemble PistonFitting PistonFitting Piston RingsInstall Piston RingsFig. 16. Piston Ring Installation Instructions.CONNECTING RODFig. 2. Magnetic Particle Inspection Limits for Connecting Rod.Fig. 3 - Dimensional Inspection of Cross-Head Piston Connecting RodsAssemble Connecting Rod to PistonCONNECTING ROD BEARINGSInstall Connecting Rod Bearing ShellsCYLINDER LINERInspect Used Cylinder LinerLiner MeasurementsSelection of New Cylinder LinerNEW CYLINDER LINER TO NEW CYLINDER BLOCK BORE FITSFitting Cylinder Liner in Block BoreFig. 11. Checking Distance of Liner Flange Below Top Face of BlockInstall Piston and Connecting Rod AssemblyInstall Cylinder Liner, Piston and Connecting Rod AssemblyENGINE BALANCE AND BALANCE WEIGHTSInstall Front Balance WeightsGEAR TRAIN AND ENGINE TIMINGENGINE TIMINGFig. 3. Checking Engine Timing By Measuring Injector DepressionCAMSHAFT, BALANCE SHAFT AND BEARINGSFig. 2. Woodruff Keys for Current CamshaftsRemove Camshaft or Balance ShaftDisassemble Camshaft and Balance ShaftInspection - TM-5-3895-359-14-P0261Fig. 10. Typical Camshaft and Balance Shaft Details and Relative Location of PartsAssemble Camshaft and Balance ShaftInstall Camshaft and Balance ShaftFig. 13. Camshaft Intermediate Bearing Lock ScrewsCAMSHAFT AND BALANCE SHAFT GEARSInstall Camshaft and Balance Shaft GearsIDLER GEAR AND BEARING ASSEMBLYFig. 3. Idler Gear Details and Relative Locating Parts (Current Bearing)Assemble Idler Gear, Hub and BearingCheck Pre-Load of BearingInstall Idler Gear, Hub and Bearing AssemblyInstall Idler Gear, Hub and Bearing Assembly (cont)CRANKSHAFT TIMING GEARBLOWER DRIVE GEAR AND SUPPORT ASSEMBLYRemove Blower Drive Gear and Support Assembly (Flywheel Housing Removed)Assemble Blower Drive Gear and Support AssemblyInstall Blower Drive Gear and Support AssemblyACCESSORY DRIVEInstall Accessory DriveBALANCE WEIGHT COVERSHOP NOTES - TROUBLE SHOOTING TROUBLE SHOOTING - TM-5-3895-359-14-P0283TABLE OF SPECIFICATIONS, NEW CLEARANCES AND WEAR LIMITS - TM-5-3895-359-14-P0284Cross-Head Pistons and Rings 71N EnginesPiston Pins (Cross-Head Piston)Camshaft and Balance Shaft BearingsExhaust Valves - TM-5-3895-359-14-P0288STANDARD BOLT AND NUT TORQUE SPECIFICATIONS - TM-5-3895-359-14-P0289EXCEPTIONS TO STANDARD BOLT AND NUT TORQUE SPECIFICATIONS - TM-5-3895-359-14-P0290EXCEPTIONS TO STANDARD BOLT AND NUT TORQUE SPECIFICATIONS (Cont)SPECIAL PLUG TORQUE SPECIFICATIONSSERVICE TOOLS - TM-5-3895-359-14-P0293SERVICE TOOLS (cont)Chapter 3: FUEL SYSTEM AND GOVERNORFUEL INJECTOR (Needle Valve)Operation - TM-5-3895-359-14-P0298Fig. 5 Injector Identification ChartGeneral Instructions for Injector Care and OverhaulRemove InjectorInjector Control Rack and Plunger Movement TestVisual Inspection of PlungerFig. 14 Assembling Injector Valve Parts on Tip Tester Adaptor J 23010-129Injector Pressure Holding TestNeedle Valve Lift TestFuel Output TestFig. 19. Fuel Output ChartFig. 22 Setting Calibrator Stroke CounterFig. 27. Cleaning injector Spray TipClean Injector PartsFig. 33. Lapping Spray Tip on Lapping Blocks JInspect Injector PartsFig. 37. Injector Plunger, Follower and Relative Location of PartsTABLE 1. Minimum Thickness (Used Parts)ASSEMBLE INJECTORFig. 43. Checking Injector Spray Tip Concentricity using Tool J 29584Assemble Plunger and FollowerInstall InjectorFUEL INJECTOR TUBEReam Injector TubeFig. 5 - Reaming Injector Tube for Injector NutReam the bevel seat in the injector tubeFUEL PUMPOperation - TM-5-3895-359-14-P0325Fig. 3 - Fuel Pump Valving and Rotation (Right-Hand Pump)Disassemble Fuel PumpAssemble Fuel PumpInstall Fuel PumpFig. 10 Installing Drive Shaft and Gear AssemblyFUEL STRAINER AND FUEL FILTERFUEL MANIFOLDMECHANICAL GOVERNORVARIABLE SPEED MECHANICAL GOVERNORDisassemble GovernorFig. 2 - Variable Speed Governor MountingFig. 4 - Removing Bearings from Cover using ToolInspection - TM-5-3895-359-14-P0338Assemble Governor CoverAssemble Governor Control' HousingAssemble Variable Speed Spring HousingFig. 13. Variable Speed Spring Housing and Shaft Details and Relative Location of PartsAssemble Variable Speed Spring Housing to the Control HousingInstall GovernorFUEL INJECTOR CONTROL TUBEInstall Injector Control TubeINJECTOR CALIBRATOR READINGSREFINISH LAPPING BLOCKSINJECTOR TIMINGREFINISHING INJECTOR FOLLOWER FACEPRESSURIZE FUEL SYSTEM CHECK FOR LEAKSTROUBLE SHOOTING - TM-5-3895-359-14-P0352CHECKING FUEL FLOWTROUBLE SHOOTING CHARTS (Needle Valve Injectors)INSUFFICIENT INJECTOR HOLDING TIMEINCORRECT INJECTOR OUTPUTSTANDARD BOLT AND NUT TORQUE SPECIFICATIONS - TM-5-3895-359-14-P0357EXCEPTIONS TO STANDARD BOLT AND NUT TORQUE SPECIFICATIONS - TM-5-3895-359-14-P0358SERVICE TOOLS - TM-5-3895-359-14-P0359INJECTOR TUBEChapter 4: AIR INTAKE SYSTEMAIR CLEANERService - TM-5-3895-359-14-P0364Element LifeAIR SHUTDOWN HOUSINGInstall Air Shutdown HousingBLOWERFig. 1 - Blower and Drive Assembly and Accessories including Mechanical Governor Attached to blowerRemove Accessories from BlowerDisassemble BlowerInspection - TM-5-3895-359-14-P0372Fig. 7 - Typical Details and Relative Location of PartsAssemble BlowerFig. 10 - Position of Blower Front End Plate on HousingInstall Blower Rotor Shaft Bearings and GearsFig. 14 - Installing Ball Bearing on Rotor Shaft and in Rear End Plate using Tool J 6270-7.Fig. 16 - Measuring "CC" and "C" Clearances Between Blower Rotor Lobes.Fig. 17 - Chart of Minimum Clearances for Blowers.Fig. 18 - Diagram Showing Proper Location of Shims for Correct Rotor Lobe Clearances.Attach Accessories to BlowerINSTALLING WATER PUMP DRIVE AND ROTOR SHAFT KITInstall Service Rotor Front Stub ShaftTABLE OF SPECIFICATIONS, NEW CLEARANCES AND WEAR LIMITS - TM-5-3895-359-14-P0384STANDARD BOLT AND NUT TORQUE SPECIFICATIONS - TM-5-3895-359-14-P0385EXCEPTIONS TO STANDARD BOLT AND NUT TORQUE SPECIFICATIONS - TM-5-3895-359-14-P0386SERVICE TOOLS - TM-5-3895-359-14-P0387Chapter 5: LUBRICATION SYSTEMFig. 1 - Schematic Diagram of Typical Lubrication System.Lubrication System MaintenanceOIL PUMP - TM-5-3895-359-14-P0391Fig. 2 - Typical Oil Pump Mounting.Remove Oil PumpDisassemble Oil PumpAssemble Oil PumpRemove Oil Pump Driving Gear from CrankshaftInstall Oil Pump Driving Gear on CrankshaftInstall Oil PumpLUBRICATING OIL PRESSURE REGULATORAssemble Oil Pressure RegulatorLUBRICATING OIL FILTERReplace Spin-On FilterOIL COOLERPressure Check Oil Cooler CoreInstall Lubricating Oil CoolerLUBRICATING OIL COOLER BYPASS VALVEOIL LEVEL DIPSTICKOIL PANVENTILATING SYSTEMSTANDARD BOLT AND NUT TORQUE SPECIFICATIONS - TM-5-3895-359-14-P0410EXCEPTIONS TO STANDARD BOLT AND NUT TORQUE SPECIFICATIONS - TM-5-3895-359-14-P0411SERVICE TOOLS - TM-5-3895-359-14-P0412Chapter 6: COOLING SYSTEMENGINE COOLING SYSTEM MAINTENANCECooling System CapacityMiscellaneous Cooling SystemLUBRICATION SYSTEM - TM-5-3895-359-14-P0418WATER PUMPDisassemble Water PumpAssemble Water PumpInstall Water PumpWATER MANIFOLDTHERMOSTATInstall ThermostatRADIATORRemove RadiatorCOOLANT PRESSURE CONTROL CAPENGINE COOLING FANDisassemble Fan, Hub and BracketAssemble Fan, Hub and BracketSTANDARD BOLT AND NUT TORQUE SPECIFICATIONS - TM-5-3895-359-14-P0432EXCEPTIONS TO STANDARD BOLT AND NUT TORQUE SPECIFICATIONS - TM-5-3895-359-14-P0433Chapter 7. EXHAUST SYSTEMEXHAUST MANIFOLDInspection - TM-5-3895-359-14-P0436Chapter 8: ELECTRICAL EQUIPMENT, INSTRUMENTS AND PROTECTIVE SYSTEMSBATTERY-CHARGING ALTERNATORALTERNATOR PRECAUTIONSTROUBLESHOOTING PROCEDUREABNORMAL CHARGING SYSTEM OPERATIONRotor Field Winding ChecksRectifier Bridge CheckSlip Ring ServicingFig. 15 - Connections for Generator Bench CheckSTORAGE BATTERY(S)Battery Safety PrecautionsSprag Overrunning Clutch Type Starting MotorFlywheel Ring GearsInterpreting Results of TestsFIELD COIL CHECKSReassembly - TM-5-3895-359-14-P0453Install Starting MotorINSTRUMENTS AND TACHOMETER DRIVEThrottle ControlInstall Tachometer DriveENGINE PROTECTIVE SYSTEMCOLD WEATHER STARTING\ALIGNMENT TOOLS FOR TACHOMETER DRIVE COVERS AND ADAPTORSSTANDARD BOLT AND NUT TORQUE SPECIFICATIONS - TM-5-3895-359-14-P0461EXCEPTIONS TO STANDARD BOLT AND NUT TORQUE SPECIFICATIONS - TM-5-3895-359-14-P0462SERVICE TOOLS - TM-5-3895-359-14-P0463Chapter 9: OPERATING CONDITIONSENGINE RUN-IN INSTRUCTIONSDynamometerENGINE TEST REPORTBASIC ENGINE RUN-ININSPECTION AFTER FINAL RUN-INFUEL OILS FOR DETROIT DIESEL ENGINESFUELS BURNED IN DETROIT DIESEL ENGINESLUBRICATING OILS FOR DETROIT DIESEL ENGINESVISCOSITY GRADE AND OIL PERFORMANCE LEVELSYNTHETIC OILSSTATEMENT OF POLICY ON FUEL AND LUBRICANT ADDITIVESENGINE COOLANTCORROSION INHIBITORS VITALINHIBITOR SYSTEMSTEST STRIPSGENERAL RECOMMENDATIONSChapter 10. ENGINE TUNE-UPEXHAUST VALVE CLEARANCE ADJUSTMENTFUEL INJECTOR TIMINGVARIABLE SPEED MECHANICAL GOVERNOR AND INJECTOR RACK CONTROL ADJUSTMENTFig. 3 - Buffer and Idle Speed Adjusting ScrewAdjust /Maximum No-Load SpeedAdjust Idle SpeedChapter 11. PREVENTIVE MAINTENANCE TROUBLE SHOOTING - STORAGE - PLUGGING CHARTSENGINE OIL CHANGE INTERVALSDiesel Fuel ContaminationReplace all belts in a set when one is worn.Item 15 - Emergency ShutdownItem 20 - Fuel Injectors and Valve ClearanceItem 27 - Crankcase BreatherTROUBLE SHOOTING - TM-5-3895-359-14-P0497Fig. 2 - Checking Compression PressureEngine Out of FuelAir Box PressurePROPER USE OF MANOMETERExhaust Smoke Analysis - TM-5-3895-359-14-P0502EXHAUST SMOKE ANALYSIS - TM-5-3895-359-14-P0503Hard StartingSUGGESTED REMEDY - TM-5-3895-359-14-P0505Abnormal Engine Operation SUGGESTED REMEDY - TM-5-3895-359-14-P0507No Fuel or Insufficient FuelSUGGESTED REMEDY - TM-5-3895-359-14-P0509Abnormal Engine Coolant Operating Temperature Excessive Crankcase Pressure Low Oil Pressure SUGGESTED REMEDY - TM-5-3895-359-14-P0513HIGH LUBRICATING OIL CONSUMPTIONSUGGESTED REMEDY - TM-5-3895-359-14-P0515PREPARING ENGINE FOR STORAGEPROCEDURE FOR RESTORING AN ENGINE TO SERVICE WHICH HAS BEEN IN EXTENDED STORAGEPLUGGING CHARTS LC and RC ENGINESPLUGGING CHARTS LC and RC ENGINES (Cont)SUBSECTION 11 FRONT AXLE AND STEERINGINSTALLATION AND OPERATIONHYDRAULIC FLUID RECOMMENDATIONSSERVICE INSPECTION AND MAINTENANCETABLE II - TROUBLE SHOOTING CHARTREASSEMBLY - TM-5-3895-359-14-P0526STEERING GEAR REPLACEMENTFRONT AXLE REPAIRSUBSECTION 12 STEERING CYLINDERPOWER STEERING VALVE UNIT ON STEERING COLUMNSUBSECTION 13 V.P.I. FLUID HANDLING SYSTEMCALIBRATING THE V.P.I. SYSTEMMETER RECORDING UNITFIGURE 5TRAVEL SPEED UNITFIGURE 8SUGGESTED EXTERNAL POWER SOURCE CIRCUITRYV.P.I. TROUBLE SHOOTINGSUBSECTION 14 GASOLINE PUMP ENGINEMAGNETO BREAKER POINT ADJUSTMENTFIGURE 6. MAGNETO TIMING DIAGRAMRESTORING COMPRESSIONKEEPING ENGINE CLEANCOMPRESSIONENGINE KNOCKSCARBURETOR AND MANIFOLDGEAR COVERFIGURE 18CYLINDER BLOCKSCAMSHAFTGOVERNOR OPERATIONWALBRO CARBURETOR - TM-5-3895-359-14-P0552ENGINE SMOKES AND RUNS RICHFIGURE 31. EXPLODED VIEW Instructions and Service Parts IllustrationSUBSECTION 15 LUBRICATION CHARTSLUBRICATION CHART 1 - GENERAL LUBRICATION CHART 2 - EMULSION HANDLING SYSTEMFIG. 1. ROTOR HOOD, TAILBOARD, LIFT ARMS, HOOD ARMS, JACK AXLE ARMR AND SKISROTOR HOOD-CRANE-TAILBOARD-LIFT ARMS HOOD ARMS-JACK AXLE ARMS & SKIS REX SELF-PROPELLED PULVI MIXERSFIG. 2. ROTOR ASSEMBLYFIG. 3. ROTOR DRIVE CHAIN CASE (LEFT AND RIGHT REQUIRED)ROTOR DRIVE CHAIN CASE (TWO REQUIRED)FIG. 4. ROTOR DRIVE LINEROTOR DRIVELINES TRANSMISSION TO ROTOR DRIVE AXLE- ROTOR DRIVE AXLE SUPPORT ARMSFIG. 5. EMULSION PUMP ASSEMBLY PEABODY - BARNES MODELS: 30CCG, 30CCG-1, 30CCG-2EMULSION PUMP ASSEMBLY PEABODY - BARNESFIG. 6. PUMP FOR WASH-DOWN SYSTEMFIG. 7. EMULSION HANDLING UNIT PIPING, CONTROLS HYDRAULIC LINES AND FITTINGSEMULSION HANDLING UNIT PIPING - CONTROLS - HYDRAULIC LINES & FITTINGSEMULSION HANDLING UNIT PIPING - CONTROLS - HYDRAULIC LINES & FITTINGS (Cont) - TM-5-3895-359-14-P0571EMULSION HANDLING UNIT PIPING - CONTROLS - HYDRAULIC LINES & FITTINGS (Cont) - TM-5-3895-359-14-P0572FIG. 8. FLOW METERFLOW METER AND TACHOMETER GENERATOR ASSY. 4' MODEL 4MLFT- SGHFLOW METER AND TACHOMETER GENERATOR ASSY. 4' MODEL 4MLFT- SGH (Cont)FIG. 9. WATER AND ASPHALT SPRAY BARS AND ROTOR HOOD COVERSWATER AND ASPHALT SPRAY BARS AND ROTOR HOOD COVERS REX SELF PROPELLED PULVI MIXERSFIG. 10. TRACTION DRIVE WHEEL ENDS AND BRAKESTRACTION DRIVE WHEEL ENDS INCLUDED IN AXLE ASSEMBLY 102-6168-1 ROCKWELL MODEL TA-279-HXI EFFECTIVE HK-381TRACTION DRIVE WHEEL ENDS INCLUDED IN AXLE ASSEMBLY 102-6168-1 ROCKWELL MODEL TA-279-HXI EFFECTIVE HK-381 (Cont)FIG. 11. TWO SPEED TRANSMISSION - ROTOR DRIVEROTOR DRIVE TWO-SPEED TRANSMISSION REX PART NO. 602-10224-2 ROTOR DRIVE CLUTCH ASSEMBLY REX PART NO. 102-9080-1 LIPE ROLLWAY CORP. 150-61-73ROTOR DRIVE TWO-SPEED TRANSMISSION REX PART NO. 602-10224-2 ROTOR DRIVE CLUTCH ASSEMBLY REX PART NO. 102-9080-1 LIPE ROLLWAY CORP. 150-61-73 (Cont)FIG. 12. TRACTION DRIVE TRANSMISSION (2 SPEED)TRACTION DRIVE TWO-SPEED TRANSMISSION INCLUDED IN AXLE ASSEMBLY 102-11053-1 MODEL NO. PRTA 592 H200 WITH NOSE BOXFIG. 13. TRACTION DRIVE AXLEDIFFERENTIAL, CASE AND HOUSING INCLUDED IN AXLE ASSEMBLY 102-11053-1 MODEL NO. PRTA 592 H200 w/NOSE BOXFIG. 14. ROTOR DRIVE AXLEROTOR DRIVE AXLE ROCKWELL STANDARD MODEL JH-150-X-48 DWG. 35-1019 Axle Assembly 102-0154-01ROTOR DRIVE AXLE ROCKWELL STANDARD MODEL JH-150-X-48 DWG. 35-1019 Axle Assembly 102-0154-01 (Cont) - TM-5-3895-359-14-P0590ROTOR DRIVE AXLE ROCKWELL STANDARD MODEL JH-150-X-48 DWG. 35-1019 Axle Assembly 102-0154-01 (Cont) - TM-5-3895-359-14-P0591FIG. 15. TRACTION DRIVE PUMPFIG. 16. TRACTION DRIVE PUMP WITH UNIVERSAL JOINT CONNECTIONS (FRONT OF DIESEL)FIG. 17. TRACTION DRIVE MOTORFIG. 18. TRACTION DRIVE HYDRAULIC LINESHYDRAULIC LINES & FITTINGS - TRACTION DRIVE WHEELS & TIRES REX HYDROSTATIC DRIVE PULVI MIXERHYDRAULIC LINES & FITTINGS - TRACTION DRIVE WHEELS & TIRES REX HYDROSTATIC DRIVE PULVI MIXER (Cont)FIG. 19. HYDRAULIC PUMP FOR TAILBOARD - SPRAY BAR AND CRANE RAMSFIG. 20. HYDRAULIC CONTROL VALVE FOR TAILBOARD AND ROTOR LIFT RAMSHYDRAULIC CONTROL VALVE FOR ROTOR HOIST RAM AND TAILBOARD CONTROL RAMFIG. 21. MODEL V20 DIRECTIONAL CONTROL VALVE TYPICAL MAIN ASSEMBLYFIG. 22. 4-WAY, 3-POSITION VALVE SECTIONFIG. 23. STANDARD SPOOL POSITIONERFIG. 25. OPTIONAL VERTICAL HANDLE AND BRACKET ASSEMBLYFIG. 26. LOAD CHECK PLUG ASSEMBLYFIG. 27. MODEL RDSON MAIN RELIEF VALVE (NON-ADJUSTABLE)Standard Buna-N Seals and O-RingsFIG. 28. HYDRAULIC LINES - VALVE TO SPRAY BARFIG. 29. HYDRAULIC LINES SCHEMATIC FOR ROTOR AND TAILBOARDHYDRAULIC LINES SCHEMATIC ROTOR & TAILBOARD LIFT FOR G.M. DIESEL POWER ONLYFIG. 30. HYDRAULIC CYLINDER FOR SPRAY BAR AND FIFTH WHEELFIG. 31. HYDRAULIC CYLINDER RAM FOR ROTOR LIFTFIG. 32. HYDRAULIC CYLINDER FOR SPRAY BAR AND FIFTH WHEELFIG. 33. HYDRAULIC CYLINDER FOR TAILBOARDFIG. 34. GENERAL MOTORS DIESEL POWER UNITGENERAL MOTORS DIESEL POWER UNITGENERAL MOTORS DIESEL POWER UNIT - CONTINUED - TM-5-3895-359-14-P0617GENERAL MOTORS DIESEL POWER UNIT - CONTINUED - TM-5-3895-359-14-P0618FIG. 35. POWER STEERING PUMPFIG. 36. POWER STEERING CYLINDERPOWER STEERING CYLINDER ASSEMBLYFIG. 37. FIFTH WHEEL - TACH DRIVEFIFTH WHEEL -- GEARCASE - GENERATOR VISUAL PERFORIMANCE INDICATORFIFTH WHEEL -- GEARCASE - GENERATOR VISUAL PERFORIMANCE INDICATOR (Cont)FIG. 38. EXPLODED VIEW OF ENGINEFIG. 39. MANIFOLD AND CRANKCASE GROUPMANIFOLD AND CRANKCASE GROUPFIG. 40. CRANKSHAFT, PISTON AND CONNECTING ROD GROUPCRANKSHAFT, PISTON AND CONNECTING ROD GROUPFIG. 41. CAMSHAFT AND FUEL PUMP MOUNTING GROUPFIG. 42. OIL FILTER AND OIL FILLER MOUNTING GROUPFIG. 43. AIR SHROUDINGFIG. 44. CYLINDER BLOCK ASSEMBLYFIG. 45. MAGNETO AND GEAR COVER GROUPFIG. 46. K 95 L Oil Pump AssemblyFIG. 47. T 89K-S1, GOVERNOR ASSEMBLYGOVERNOR CONTROL ASSEMBLIESFIG. 50. Q12J GASKET SETFIG. 50. STARTING MOTOR ASSEMBLYFIG. 51. STARTER MOUNTINGFig. 52. YC66D-S1 HIGH TEMP. SAFETY SWITCH KIT.Fig. 53. WALBRO CARBURETOR MODEL LUB.WALBRO CARBURETOR - TM-5-3895-359-14-P0643Fig. 54. LO-64 SIDE MOUNT AIR CLEARNER ASSEMBLY.Fig. 55. MAGNETO - Fairbanks-Morse No. FM-XZE4B7-4, Wisconsin Motor No. Y-98-C-S2 per MIL-E-11275-C Specifications.Fig. 55. MAGNETO (Cont.) - TM-5-3895-359-14-P0646Fig. 55. MAGNETO (Cont.) - TM-5-3895-359-14-P0647FIG. 56. FRONT AXLE ASEMBLY.FRONT AXLE KIT 102-9438-1 - ROCKWELL STANDARD #FC-901FIG. 57. CONTROLS.CONTROLS - THROTTLE & TRACTION - TWO-SPEED TRACTION CASE BRAKE & CLUTCH PEDAL ASSEMBLYCONTROLS - THROTTLE & TRACTION - TWO-SPEED TRACTION CASE BRAKE & CLUTCH PEDAL ASSEMBLY (Cont) - TM-5-3895-359-14-P0652CONTROLS - THROTTLE & TRACTION - TWO-SPEED TRACTION CASE BRAKE & CLUTCH PEDAL ASSEMBLY (Cont) - TM-5-3895-359-14-P0653FIG. 58. MAIN FRAME, ENGINE HOUSE, FLOORBOARD AND FENDERS.MAIN FRAME - ENGINE HOUSE - FLOORBOARD- FENDERSMAIN FRAME - ENGINE HOUSE - FLOORBOARD- FENDERS (Cont)FIG. 59. FUEL TANK FOR DIESEL ENGINE AND OPERATOR'S SEAT.DECALS AND LABELS REX SELF PROPELLED PULVI MIXERFIG. 61. WIRING SCHEMATIC - LIGHTING.SECTION 3 PARTS INDEX (Cont)SECTION 3 PARTS INDEX (Cont) Section 4: SUPPLEMENTAL OPERATING, MAINTENANCE AND REPAIR PARTS INSTRUCTIONS FOR MIXER, ROTARY TILLER, SOIL STABILIZATION: MODEL HDS-ESUBSECTION I GENERAlPersonnel and TrainingSUBSECTION II MAINTENANCEMaintenance Expenditure LimitsSUBSECTION III REPAIR PARTS SUPPLYRequisitioning Repair Parts.APPENDIX A: EQUIPMENT PUBLICATIONSAppendix B: WARRANTY GUIDELINESAPPENDIX B (Cont'd)APPENDIX C: MAINTENANCE ALLOCATION CHART FOR MIXER, ROTARY TILLER, SELF-PROPELLEDColumn EntriesColumn Entries (Cont)Section II. MAINTENANCE ALLOCATION CHART - TM-5-3895-359-14-P0677Section II. MAINTENANCE ALLOCATION CHART (Cont) - TM-5-3895-359-14-P0678Section II. MAINTENANCE ALLOCATION CHART (Cont) - TM-5-3895-359-14-P0679Section II. MAINTENANCE ALLOCATION CHART (Cont) - TM-5-3895-359-14-P0680Section II. MAINTENANCE ALLOCATION CHART (Cont) - TM-5-3895-359-14-P0681Section II. MAINTENANCE ALLOCATION CHART (Cont) - TM-5-3895-359-14-P0682Section II. MAINTENANCE ALLOCATION CHART (Cont) - TM-5-3895-359-14-P0683Section II. MAINTENANCE ALLOCATION CHART (Cont) - TM-5-3895-359-14-P0684Section II. MAINTENANCE ALLOCATION CHART (Cont) - TM-5-3895-359-14-P0685Section II. MAINTENANCE ALLOCATION CHART (Cont) - TM-5-3895-359-14-P0686Section II. MAINTENANCE ALLOCATION CHART (Cont) - TM-5-3895-359-14-P0687Section II. MAINTENANCE ALLOCATION CHART (Cont) - TM-5-3895-359-14-P0688Section II. MAINTENANCE ALLOCATION CHART (Cont) - TM-5-3895-359-14-P0689Section II. MAINTENANCE ALLOCATION CHART (Cont) - TM-5-3895-359-14-P0690Section II. MAINTENANCE ALLOCATION CHART (Cont) - TM-5-3895-359-14-P0691Section II. MAINTENANCE ALLOCATION CHART (Cont) - TM-5-3895-359-14-P0692APPENDIX C: MAINTENANCE ALLOCATION CHART FOR MIXER ROTARY TILLER MODEL: HDS-ESECTION III - TOOL AND TEST EQUIPMENT REQUIREMENTSAPPENDIX C: Section IV Remarks Mixer, Rotary Tiller, Self-Propelled Reworks Model HDS-EAPPENDIX D: CCE MANUFACTURER FIELD CAMPAIGNS AND MODIFICA-ION PROCEDURESAPPENDIX E: BASIC ISSUE ITEMS LISTAPPENDIX G: INITIAL RECOMMENDATION PRESCRIBED LOAD LIST (PLL) AUTHORIZED STOCKAGE LIST (ASL)APPENDIX G: INITIAL RECOMMENDATION PRESCRIBED LOAD LIST (PLL) AUTHORIZED STOCKAGE LIST (ASL) (Cont)APPENDIX H: SECTION MAINTENANCE AND OPERATING SUPPLY LISTAPPENDIX H: SECTION MAINTENANCE AND OPERATING SUPPLY LIST (Cont)Appendix I: REQUISITION PROCESSING GENERAL INSTRUCTIONSNon-NSN Requisition (Manual) Table H: NON-NSN REQUISITION FORMATAppendix J: PREVENTATIVE MAINTENANCE CHECKS AND SERVICES (PMCS)OPERATOR/CREW AND ORGANIZATIONAL MAINTENANCE CHECKS AND SERVICES.OPERATOR/CREW AND ORGANIZATIONAL MAINTENANCE CHECKS AND SERVICES. (Cont)OPERATOR /CREW PREVENTIVE MAINTENANCE CHECKS AND SERVICES (PMCS)OPERATOR /CREW PREVENTIVE MAINTENANCE CHECKS AND SERVICES (PMCS) (Cont) - TM-5-3895-359-14-P0709OPERATOR /CREW PREVENTIVE MAINTENANCE CHECKS AND SERVICES (PMCS) (Cont) OPERATOR /CREW PREVENTIVE MAINTENANCE CHECKS AND SERVICES (PMCS) (Cont) - TM-5-3895-359-14-P0711ORGANIZATIONAL PREVENTIVE MAINTENANCE CHECKS AND SERVICESORGANIZATIONAL PREVENTIVE MAINTENANCE CHECKS AND SERVICES (Cont) - TM-5-3895-359-14-P0713ORGANIZATIONAL PREVENTIVE MAINTENANCE CHECKS AND SERVICES (Cont) - TM-5-3895-359-14-P0714TM-5-3895-359-14-P Mixer Rotary Tiller Soil Stabilization Reworks Model HDS-E Diesel Engine Driven (DED) Manual
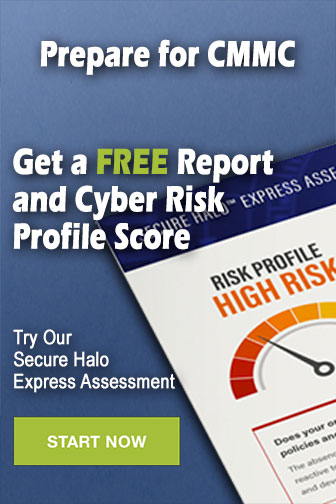